Preparing the Alioth
- Dec 24, 2023
- 5 min read
I purchase an Alioth just after the MYA AGM. The boat was the result of a cancelled order and I was keen to try what could be described as a standard albeit high quality build from Paul Barton who has developed considerable experience in 3D printing. It makes for an interesting winter evaluating the strengths and weaknesses of this relatively new technology.
3 D print technology has come a long way and is developing rapidly with new increasingly stronger materials. I note now that several other classes are experimenting using 3d printing tech. eg RG65, A class, Marblehead. As the guys on the 3dprintedradioyachts site observed, you can imagine a product in the morning, design it on 3d cad software and print it all within 24 hours depending on what you are building. Whatever we think about how this technology is disrupting the norms, it is here to stay, allowing home builders to reestablish themselves and designers to test new designs and potentially test them on the water in 24 hours. Thank god that the design iteration of the IOM seems to be near maturity otherwise we would be back in a design race.
Whilst I am rambling, wasn't it great to see two of yachtings greats sailing in the US IOM championship in the form of Ken Read and Bruce Farr both sailing Kantun's. Ken was top American but third to Zvonko (Kantun) and Ian Vickers (V12). There is a great interview with Ken Read where he compares the IOM to the TP 52 of the yachting. It was interesting to hear that Ken learnt his craft in the DF95 with 75 other club sailors. The interview is here: https://www.facebook.com/groups/200279930037252/?multi_permalinks=7261644047234103&ref=shareIt
It appears some of our top sailors cannot stay away from our sport which is good news for all.
Onto the Alioth. Several picture below
I bought a hull with Standard fin, bulb and rudder from Paul Barton. His build quality is excellent and I was so impressed I took a hammer to the hull and struck a few blows to confirm what I already knew. It was bullet proof. In fact at the MYA AGM I jumped with both feet onto a sample of the mid third of the hull and could not crack the material. There are various charts that show the comparable strengths of the various materials available today and the ones being used at the moment are robust against impact, heat and UV. How technology moves forward so quickly.
If you want to find out more take a look at the site where there are some great articles on the development of the technology and how to build your first boat plus free files on fittings and designs. They have printed a competitive A class boat.
I have deliberately not sanded the hull which has very fine marks where each layer of the print was put down but this may have a positive impact on laminar flow. We shall see. The hull has been given a coat of automotive varnish as the plastic can pick up dirt.
Structurally the hull is strong with a printed triangulation structure bracing the mast and shrouds. In fact all the components under the deck are 3 D printed bar a couple of metal load bearing tubes for the shrouds and are precisely repeatable. I cannot see or measure any deformation along the deck when the backstay is loaded up.
The jib is attached to the deck using a magnet sitting in a slot on the foredeck. The jib sheet is run through the centre of the foredeck with a single additional eye for the B and C rig. All jibs are set to 85 degrees when downwind.
The mast is secured in the step with a horizontal bar which fits into the female equivalent in the hull so the mast cannot rotate. Internally I have an RMG H1 winch with a 45mm drum and the sheeting under the deck. The spiral is great for gybing and provides precision sheeting upwind. I modified the sheeting system provided by Paul so that all was easily accessible and easy to fix in the event of a breakage.
There is a large patch at the aft end of the boat and a large pot cover above the winch. Because there is no patch forward, it is very important to vent the front of the hull and I use a pillow inflator which has the advantage of pumping warm air into the hull at speed. 5 minutes of this will dry any hull.
The rudder assembly is made of a micro servo connected to the tiller by a 1/8th carbon rod used for control rods in model aircraft.
The rig is transferred from my Britpop with the only adjustments being the mast step with the locating slot and slightly longer 62mm spreaders on the A rig and 56mm on the B rig as the shroud base is wider on the Alioth, and a new set of holes on the A jib boom to accommodate the sheeting arrangements. One thing I did note was that the main boom band is nearly 2cm above the deck as the deck profile is lower than the Britpop. Ideally I would lower this to the deck but waiting feedback from the designer. Because the shroud base is wider, I suspect I will be sailing with slacker shrouds so I can get movement in the rig in the gusts.
The boat has 80gm of correctors and this has got me thinking about the necessity of lowering the weight of the boat to get 2-300gms of correctors. So far the boat has performed competitively in a chop. More on that another day.
In the first two open meetings, even with some teething troubles which are now sorted, the boat performed well. We know it is capable of a top ten or better finish in an international regatta, so the design sits well with the Britpop, Venti, Kantun, Sedici, V11/12.
The final tweaks have been made and now it just remains to get out sailing and see how she goes against top competition. I am confident it will do well.
A few Photos
The jib boom is held under the line of the fordeck
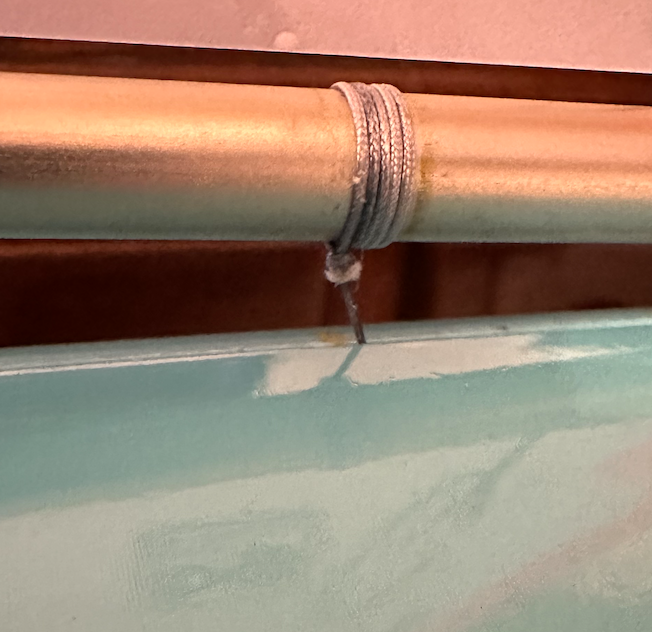
The sheeting arrangement. Any slack in the sheets when easing onto a run in light weather is held in the back of the boat away form the winch and drum ensuring there is minimal chance of foul ups. All the sheeting arrangement is easily accesible and can be changed rapidly in the event of failure.
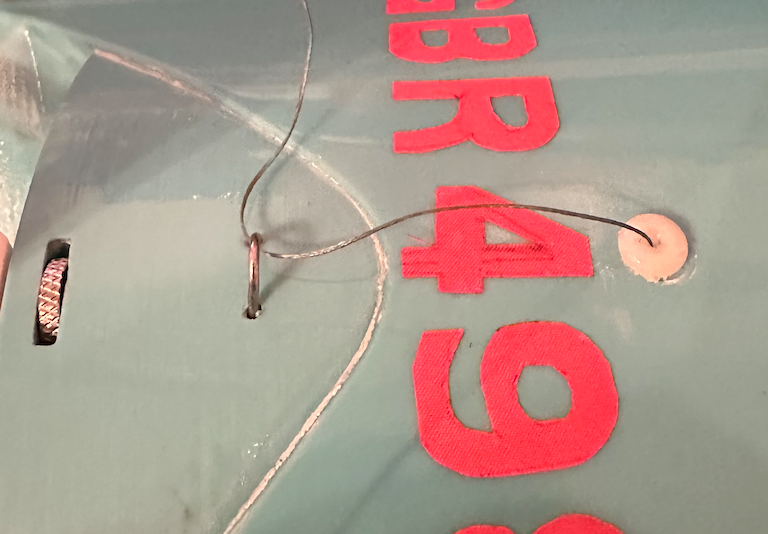
This shows where the slack sheets are held in the aft end of the boat and the carbon rod connector. I taped over the corner of the balance weights just incase the loose sheet tries to trap itself.
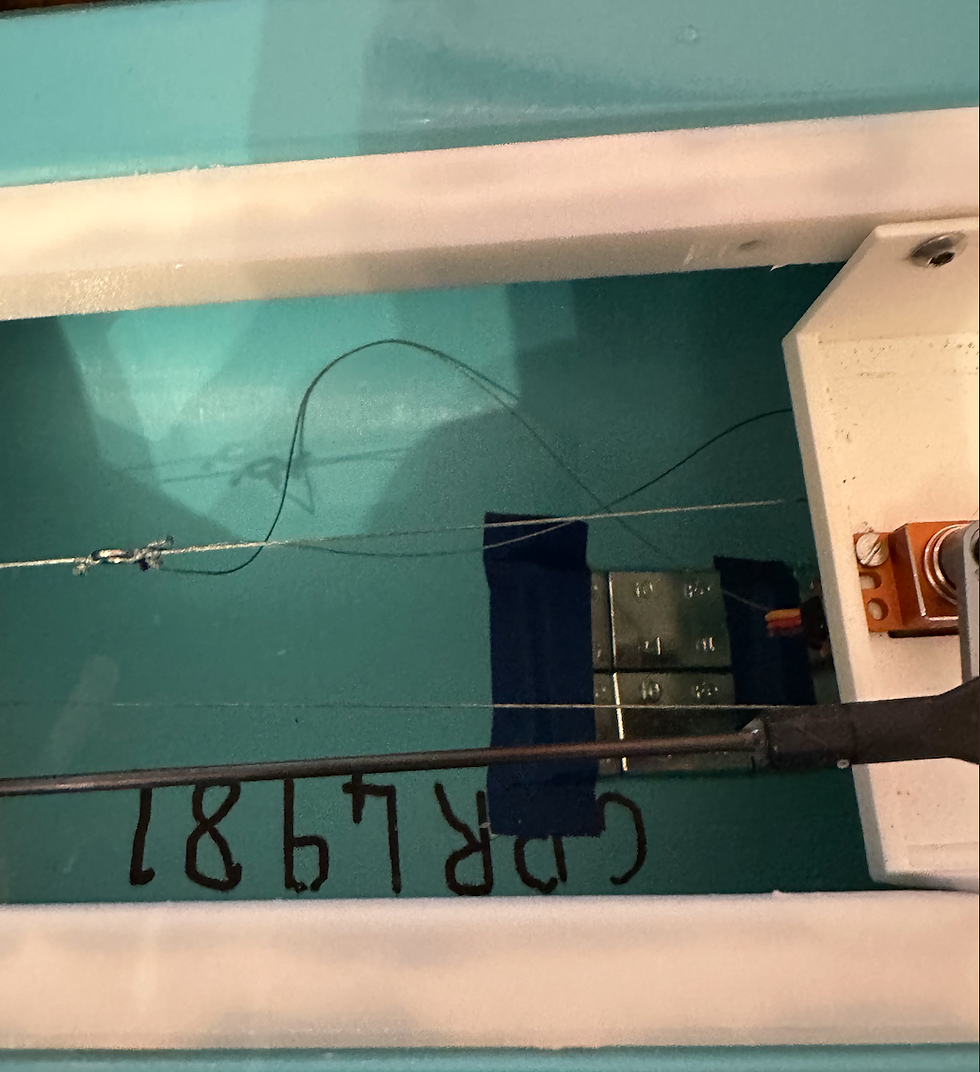
The mast ram
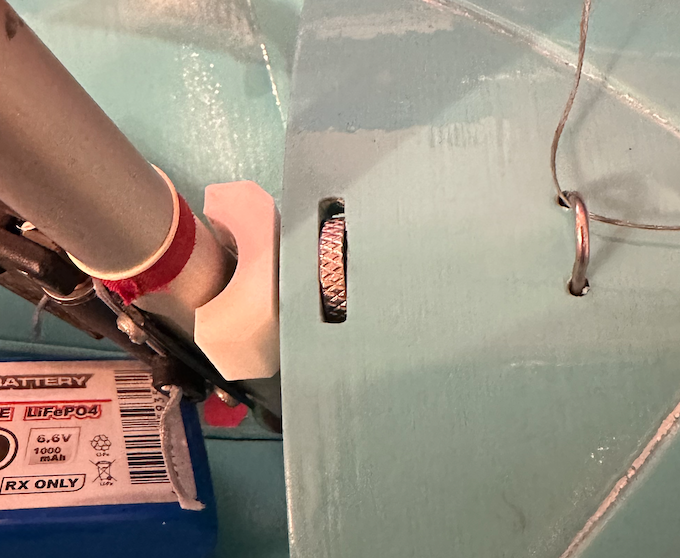
The neat mast step fitting

Early days

Comments