It is possible to have a Brand-New competitive IOM in 6 weeks for less than £1500? …. Really?
By Malcolm Appleton
Fact or fiction? I wanted to find out, because:
Like it or not we live in the Amazon generation of click and collect. What permeated the souls of Gen Z over five years ago has, supercharged by the Covid shut downs leached its way into the consciousness of the Boomer Generation.
That means for me, that prospect of waiting up 18 months for delivery of a competitive hull plus another month for final fitout (or earlier for the same price as a small car) has become unacceptably frustrating.
And it carries the risk that I may not live long enough to see it to fruition. ☹
But is there a solution? … continuous development of both 3D printers, filament materials and the ready availability of powerful CAD systems, could a well-designed 3D printed hulls be the answer to the maiden’s prayer in drastically reducing lead times.
So, I set myself the following objectives to:
-
prove that it’s possible to enter the world of International One Metre sailing with a modern design performance boat and win races for twice the price of a similar spec’d DF95. i.e. ready to sail with A, B & C rigs.
-
purchase of all components and have a finished ready to sail boat in a minimum of 4 weeks, or comfortably 6 weeks
-
find out if it was possible to build a competitive boat in my study starting from a place of never having built a boat before (feel the fear and do it anyway) and with limited model making skills plus a determination to succeed.
-
see how the boat performed in print finished form. Being lazy, i.e. not wanting to spend too much time sanding and painting the hull, I decided to research the subject of laminar flow extensively, and concluded that at the speeds a One Metre can achieve the benefit would be marginal, i.e a lot less than one badly timed tack.
Did I fulfil them? Absolutely - and this is how
I chose to build an Alioth V3 Alioth V3 - IOM ALIOTH | RC SAILING LAB on the basis that a friend at Emsworth where I sail, had already printed and built a V2 and found it to be well designed and reasonable fast.
Bribed with a bottle of finest Malt, I persuaded him to print one for me, and being a bit impulsive bought the licences just as the design had moved on to Version 3. How lucky was I!.

I built the 5-section hull and found it to perform well, but I always wanted a 3-section one with recessed jib pivots which I think look nicer.
So, I contacted Paul Barton who was happy to take my money and print a 3 section for me in a couple of weeks.
Both hulls were printed using the same Polymax PLA Tough filament which seems to be as good as its word. Temperature and speed control are important if you fancy printing your own, we found in the first endeavour one of the printed parts had suspect adhesion between the layers....not good, but rectified second time around.
Taking a deep breath, I slotted the prepared hull sections together, and they lined up precisely. Giving me the confidence to repeat the procedure this time with glue added to the joints.
When measured by Paul Edwards at Gosport the completed overall length was exactly 1 metre, and the fin and rudder lined up perfectly. Wow - this was a pleasant surprise since I did not use an assembly jig. It’s a testament to Juan Egea’s construction design.

I did use a tripod mount cross laser (Amazon £26) for ensuring the Fin was at right angles to the fore/aft water line - although strictly speaking unnecessary as the
designer’s measurements are more than adequate to achieve the same result. The laser was used because I could, (another toy for the cupboard) .
My biggest challenge for the build was choosing the correct adhesives. For non-flexible joints I used an MMA adhesive, which is a powerful hybrid Epoxy/CA mix. For the hull joints which need to flex to absorb potential collisions I use CT1 which is silicone based. I figured using a hard adhesive in a potentially flexible environment wouldn’t be a smart thing to do.
It seems to have worked – solid boat no leaks.
The printed hull was sprayed with two coats Plasticoat clear gloss, oven dried at 24 degrees (not in our kitchen oven!). Very lightly sanded in between each coat.
Initial surface prep consisted very quick light sanding with 240 grit wet and dry, afterwards simply 'washing the surface’ with Multi solve CT1 Multisolve Solvent for Removing Adhesives & Sealants (500ml) cleaner to remove surface dust and any grease.
I used this to clean the joints as well and has proven its worth.
The finished boat ready to sail required 130gms of ballast to bring it up to 4Kgs. 120gms of which I placed astride the keel box and the remainder positioned to trim the fore/aft attitude of the boat. Trimming was to the designer’s waterline specification, using the tank at Gosport.
The bare hull was fitted out using a high power DF95 rudder servo, RMG J series winch, John Gill carbon rudder (a work of art and beauty) Dave Creed Fin and Bulb, SAILSetc spars and Sailboat RC one piece moulded sails.
All the parts arrived within 3 weeks allowing me to complete the hull build in time for arrival of the sails which took just over 3 weeks to get to my doorstep for the equivalent UK sourced price.
In use, the hull has proven to be tough, substantially stronger than that of my Kantun K2 the Polymax filament proving highly resistant to accidental collision damage.
Without other distractions I calculate that the entire build would have taken me four weeks.
To conclude:
This project exceeded my expectations.
-
I learnt masses about sail settings and boat balance.
-
Ended up with a very competitive (race winning) club boat.
-
Felt the fear and did it anyway – what could possibly go wrong?
-
Mistakes are only costly in time, not £££
-
An excellent ‘value for money’ entry into One Metre sailing.
-
The downside?
-
Glue is smelly and best done in the garage
-
Glueing the parts together can be scary using a quick cure (5 min) product
-
Having to be disciplined enough to create to create time for family while building the boat.
My thanks must go to those who helped and inspired me to see the project through to its best
Chris Lawrence; Paul Barton; Nigel Barrow and Steve Taylor
Cheers guys
Author and image copyright: Malcolm Appleton January 2025

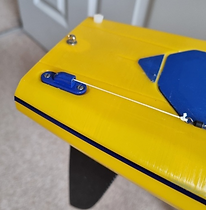